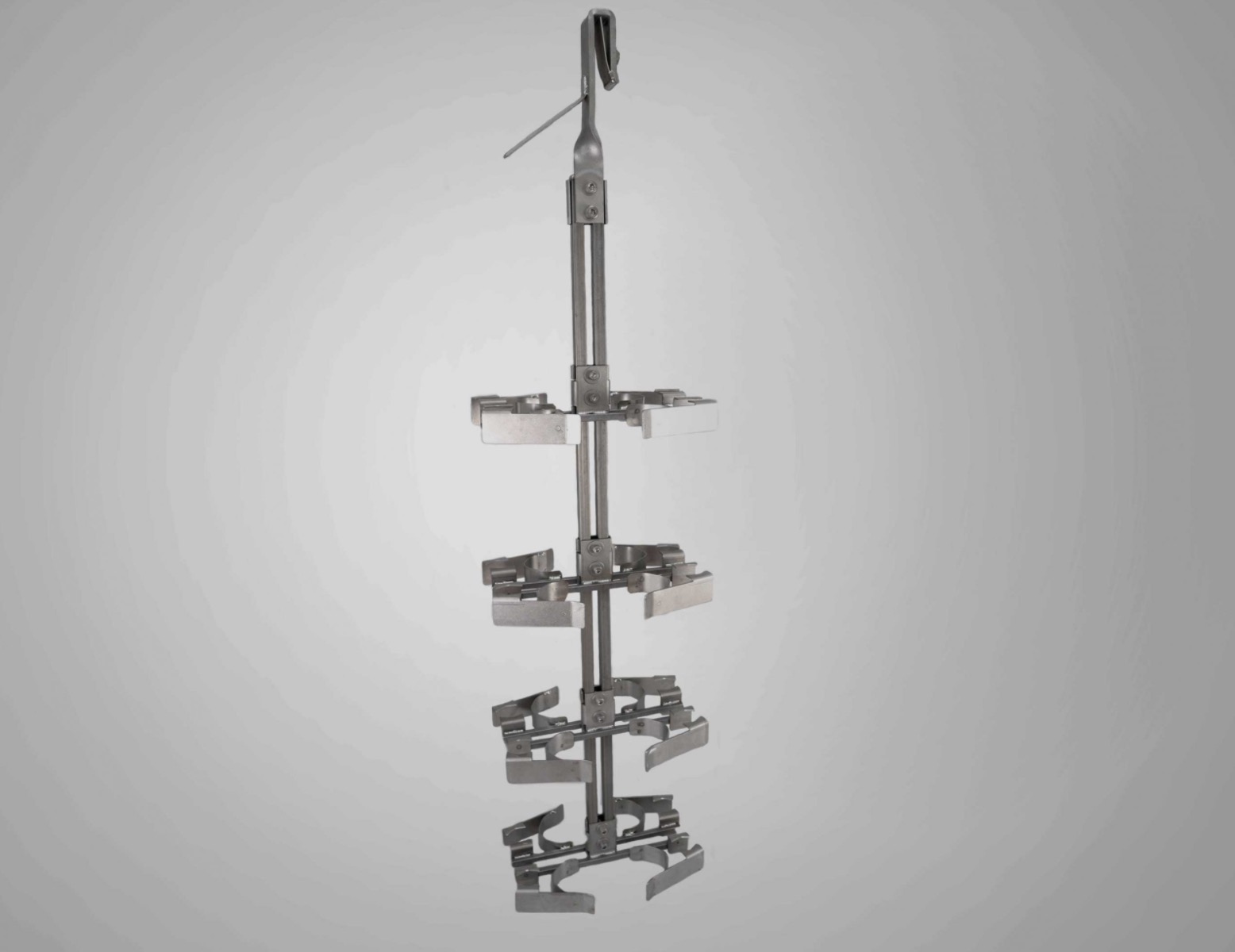
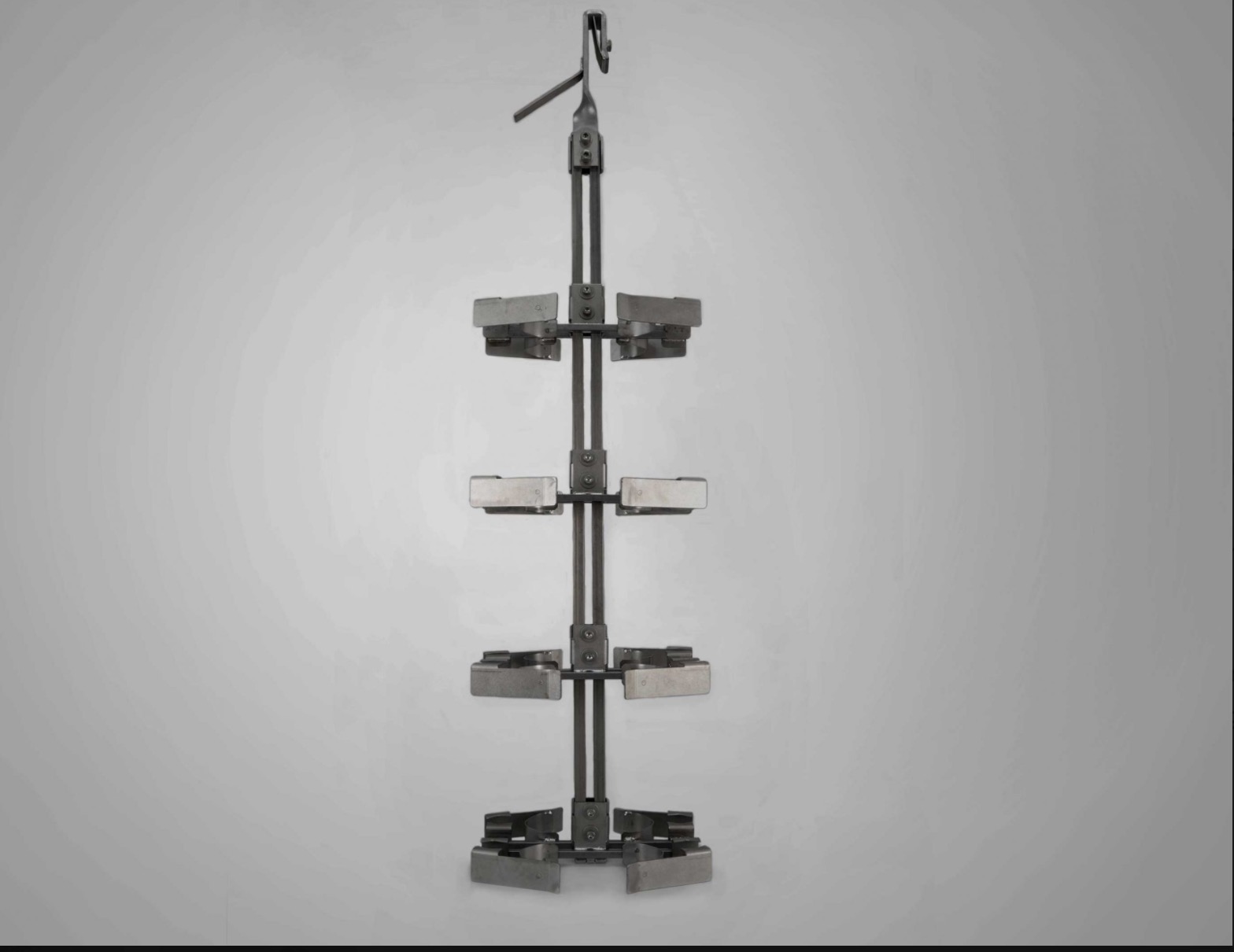
BASIC FUNCTIONS OF A JIG AND RACK
Proper jigging is a critical part of anodizing and must successfully accomplish at least three basic functions:
Hold the part securely during transfer between process tanks and while immersed in a vigorously agitated solution
Provide contacts with the work that will safely conduct enough current from the source to the part to provide a uniform coating
Provide adequate drainage of the work, leaving no pockets of residual solution trapped in the components
FACTORS IN JIG AND RACK DESIGN
The following factors need to be taken into account in jig and rack design and the way in which components are secured on racks:
1) Suitability for the process sequence and solution used
2) Ease of loading and unracking of parts
3) Prevision of secure contact points which ensure a uniform coating
4) Location of jig marks in positions acceptable to the customer
5) Density of loading of the components must balance the economics of bath loading against dangers of local overheating and shielding
6) The rack must be cost effective in terms of the quantity required and the revenue from the job
FUNCTIONAL FEATURES
The basic need is to secure properly the components on the jig and for them to be retained throughout subsequent processing. The choice of design is often a matter
of experience and judgment. The following factors have to be taken into account:
The size and weight of the part
Sensitivity of work surfaces to prevent damages from clamping
The locations where trapped gas or liquid pockets may occur
The amount of current required by the parts on the jig
The position and number of points where contact marks may be allowed
MATERIALS FOR ANODIZING JIGS AND RACKS
In the early development of anodizing racks and jigs were made exclusively of aluminium, usually pure aluminium, which had the disadvantage of being soft and readily damaged. However, this has been overcome to a large extent by the use of heat treatable alloys, such as 6061 and 2024. In high volume applications, titanium has now become widely used. Aluminium has the following advantages:
1) Low initial cost
2) Ease of fabrication
3) High level conductivity
4) Proper conductivity for electrocolouring
Offsetting these factors are the following disadvantages:
Progressive weakening by chemical attack in etching and by chemical polishing
Less robustness in handling terms